Constructability refers to the idea of optimally and strategically utilizing construction knowledge and experience in the earlier phases of a capital project, including during front-end planning, detail engineering and design, and procurement, to achieve project requirements and objectives. Effective constructability programs can:
- Reduce project cost and schedule.
- Improve overall project quality and project efficiency.
- Enhance health, safety, and environmental aspects.
- Minimize rework and schedule changes.
While it’s possible to implement constructability throughout the lifecycle of all capital projects regardless of the project delivery system (PDS), there are common barriers that frequently prevent its implementation.
Below, we detail some of these barriers and discuss constructability in turnkey projects as well as best practices to follow for optimal constructability.
Barriers to Integrating Constructability Programs
According to the Construction Industry Institute, an effective constructability program can reduce total project costs by 1-11% and total project schedules by 5-10%. However, constructability is not always incorporated throughout a capital project lifecycle. Some of the reasons for this include:
- Complacency with the status quo.
- Hesitancy to invest additional time, money, or effort in early project stages.
- The engineering and design contractor has little or no construction experience.
- Conflicting opinions or insufficient communication between the engineering and design contractor and construction contractor.
While implementing constructability in the planning and design phases of a capital project can certainly be done with any PDS, it becomes more difficult from a feasibility standpoint with design-bid-build (DBB) approaches. Lack of integration between the design and construction teams and lack of design contractor construction knowledge can make this rather challenging. However, with proper construction knowledge and effective communication and work processes, constructability can be successfully and efficiently implemented with DBB delivery systems.
Constructability in Turnkey Projects
Turnkey, also referred to as design-build or engineering, procurement, and construction (EPC), project delivery systems are particularly well-suited to integrate constructability throughout capital project lifecycles. Because projects using this PDS are completed by one team under a single contract, there is a more cohesive workflow from front-end planning through construction. All disciplines and functions work together as a highly collaborative team with the same goals and standards.
Constructability in turnkey projects should be applied across all project phases. In the front-end planning phase, constructability should be a key part of Project Execution Plans. Front-end planning should actively involve team members with strong construction experience and knowledge. The overall project design, as well as the project schedule, should be construction-driven. The design and overall layout of equipment, piping, components, and instrumentation should promote construction feasibility and efficiency as well as future site maintainability.
During the detail engineering and design phase, standardized design elements, strategically configured designs, and/or modular designs should be considered to further promote construction efficiency while taking into account personnel and equipment accessibility. The knowledge derived from incorporating constructability during detail engineering and design effectively drives procurement and fabrication needs.
Constructability Meetings: Best Practices
Once a 3D model reaches the criteria for a 30% (or phase I) model review, a constructability meeting should be organized and scheduled by the project engineer, inviting all lead engineers from each department as well as the construction manager. During the constructability meeting, each discipline weighs in and reviews critical constructability and maintainability considerations. Best practices per discipline are detailed below.
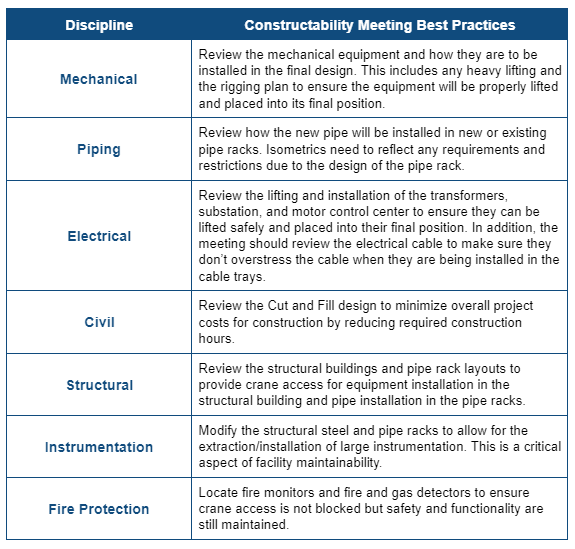
The H+M Approach
At H+M Industrial EPC, our proven work processes and highly experienced team allow us to drive your project to success while providing cost and schedule certainty. Our engineers and construction personnel have over 30 years of experience in designing and building chemical facilities. With this experience comes the understanding and dedication required to have a highly successful constructability meeting.

The H+M Industrial Team
For over three decades, we have provided best-in-class capital project management services to Energy and Chemical industries through our proven EPC approach. We are dedicated to providing trust, experience, and efficiency through all stages of engineering, procurement, and construction--on budget and on time.
Partnering with H+M Modular
H+M Modular, a division of H+M Industrial EPC, specializes in custom fabricated equipment, modules, and skids for energy and chemical industries. The approach emphasizes the potential for decreased risk through more controlled fabrication, leading to enhanced quality and safety, reduced labor costs and construction times, improved labor availability, and solutions to geographic challenges. We are dedicated to providing trust, experience, and efficiency through all stages of traditional and modular construction projects using our proven EPFC approach, If you're considering modular fabrication, we invite you to connect with us to learn about how modular solutions can improve project outcomes.