Construction quality management is an important pillar of project management for capital projects and refers to the policies, processes, and procedures put in place to provide quality assurance and quality control at construction sites.
Inspections and tests are typically conducted by internal and external inspectors to assess concrete strength, welding quality, and soil compaction, among others. Inspections aim to ensure that all capital project components are safe and up to code.
However, inspections and tests are a small part of a successful and efficient quality management system. Quality management can be the difference between project success and project failure. Let’s delve deeper into how quality management issues arise and detail essential tips for project owners.
How Do Quality Management Issues Arise?
While there are many reasons why construction quality management issues arise, some of the most common causes are as follows:
Top 10 Construction Quality Management Tips for Project Owners
To avoid quality management issues, it’s important to follow best management practices to ensure the success of your project. Below we detail our top construction quality management tips ranked according to importance.
- Implement Total Quality Management: Contractors should employ the concept of Total Quality Management (TQM) from pre-contracts through project completion. TQM is a process-oriented method used to cultivate effective collaboration, improve the quality of work, and reduce costs.
The term “total” refers to the entire contracting organization, meaning all teams, departments, and functions are involved in quality management. TQM is a managerial and technological method to achieve quality requirements and business objectives throughout the entire organization.
The key principles of TQM include customer focus, employee involvement, process centering, integrated system, strategic and systematic approach, decision-making based on facts, communication, and continuous improvement.
TQM should also include an inspection and test plan that will dictate the frequency of inspections for each discipline throughout the construction process.
Inspection Test Plans (ITPs) play a critical role in ensuring construction quality by providing a structured framework for assessing and verifying that construction activities meet specified standards and requirements. These plans help project stakeholders identify potential issues, establish clear benchmarks, and outline the necessary steps to maintain quality control throughout the construction process. By incorporating ITPs, construction projects can enhance transparency, reduce errors, and ultimately deliver a final product that aligns with the intended quality standards.
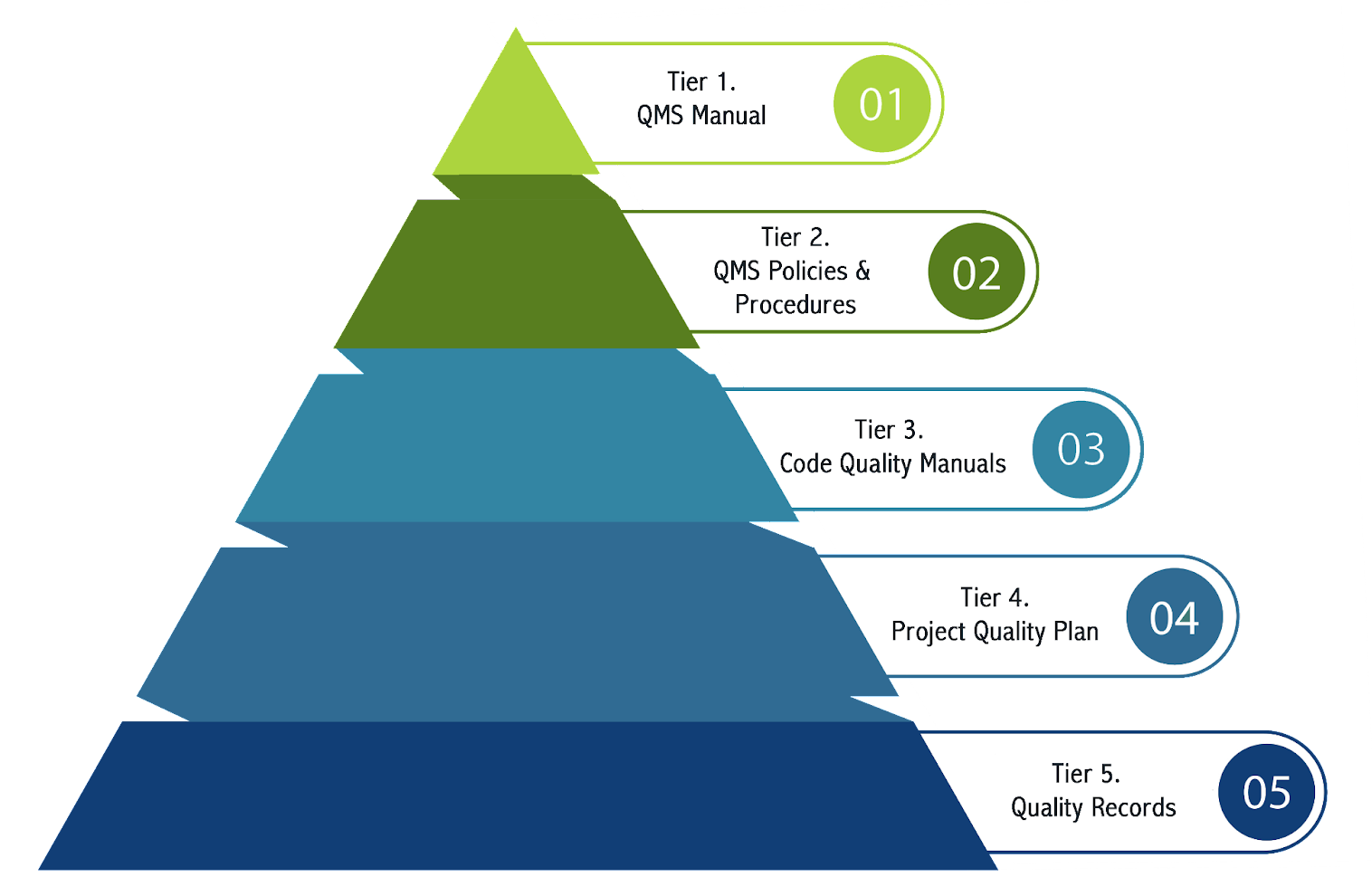
- Avoid scope growth: Scope growth can often be avoided through proper work processes such as project controls, a well-defined scope, and a solid project execution plan developed in the early stages of the project.
- Apply quality assurance processes: Contractors should engage in specific procedures to ensure the specified project quality is accomplished. Such processes should detail inspection requirements, the frequency of inspections, and documentation.
- Enact quality control programs: Contractors define the project quality that will be managed during the project's construction stage. Quality control documentation should include who is responsible for meeting quality standards and how such standards will be achieved, creating the framework for procedures and practices which ensure the completed project is on par with established quality standards.
- Ensure communication and cohesion: Work with a contractor whose teams work collaboratively as a single cohesive unit to maintain quality standards across all teams and disciplines.
- Include quality planning in kickoff meetings: Contractors should include quality planning in their kickoff meetings. This will allow for communication and alignment of the scope, inspection and test plan requirements, and execution methodology for the quality execution across the entire project team.
- Analyze individual work processes: Contractors should analyze individual work processes feeding specific activities of the job. When thoughtfully created and diligently followed, these roadmaps help drive consistent quality and ensure no steps or components are missed.
- Utilize full in-house capabilities: Contractors who have full in-house capabilities from detail engineering and design to construction can help ensure consistent quality across all project phases. Designing with a focus on constructability can provide design feasibility within the specified quality standards, schedule, and budget. This can also eliminate miscommunication issues that are often seen when multiple contractors or subcontractors are involved.
- Hire multi-disciplinary inspectors: Quality inspectors should be multidisciplinary to understand the full scope of project requirements. In other words, they should not be disciplined in a single area, such as piping or concrete but should understand the full spectrum of quality requirements.
- Use trusted vendors and suppliers: Contractors should only utilize preferred and trusted vendors and suppliers.
The H+M Approach to Construction Quality Management
At H+M Industrial EPC, we employ the concept of TQM with our core values of continuous improvement and customer satisfaction. We focus on work processes, employee training, and our feedback process through our Lesson Learned Program. Our robust and efficient QMS is scalable for all project types and sizes and is managed by our entire organization to ensure we meet or exceed your quality expectations.
To find out more about how H+M Industrial EPC can delivery high-quality construction services through our superior construction quality management processes, please fill out the following form to download our Field & Shop Inspection and Test Plan template below.

The H+M Industrial Team
For over three decades, we have provided best-in-class capital project management services to Energy and Chemical industries through our proven EPC approach. We are dedicated to providing trust, experience, and efficiency through all stages of engineering, procurement, and construction--on budget and on time.
Partnering with H+M Modular
H+M Modular, a division of H+M Industrial EPC, specializes in custom fabricated equipment, modules, and skids for energy and chemical industries. The approach emphasizes the potential for decreased risk through more controlled fabrication, leading to enhanced quality and safety, reduced labor costs and construction times, improved labor availability, and solutions to geographic challenges. We are dedicated to providing trust, experience, and efficiency through all stages of traditional and modular construction projects using our proven EPFC approach, If you're considering modular fabrication, we invite you to connect with us to learn about how modular solutions can improve project outcomes.