Industrial construction is growing. When I started working in construction in the early ’80s, the discussion about multibillion-dollar construction projects focused on the nuclear construction sector. Now, it’s common to hear about multibillion-dollar projects in every construction sector. Project values are increasing in renewables, power, and even in the smaller sectors of petrochemical and midstream.
A method to complete these projects is using a full EPC company instead of piecemealing it out using subcontractors. Managing multiple subcontractors brings its own set of problems from a quality standpoint. Full EPC companies are better in terms of Total Quality Management in construction, which leads to better productivity and cost savings.
Comprehensive Training in Total Quality Management in Construction
With the industry shift comes more client sophistication and quality requirements. No longer are quality programs solely driven by the clients’ QMS program but, more often, clients want to know what contractors have established within their own QMS program. This “skin in the game” approach by clients has driven the need to establish more vigorous training for Quality Professionals.
The construction culture is changing to incorporate a TQM approach or Total Quality Management in construction to quality. The ability to deliver quality products and services to our internal and external clients can be directly related to proving that quality oversite is established and that the folks performing that oversite are ready and qualified. The "one certification fits all" approach is no longer viable.
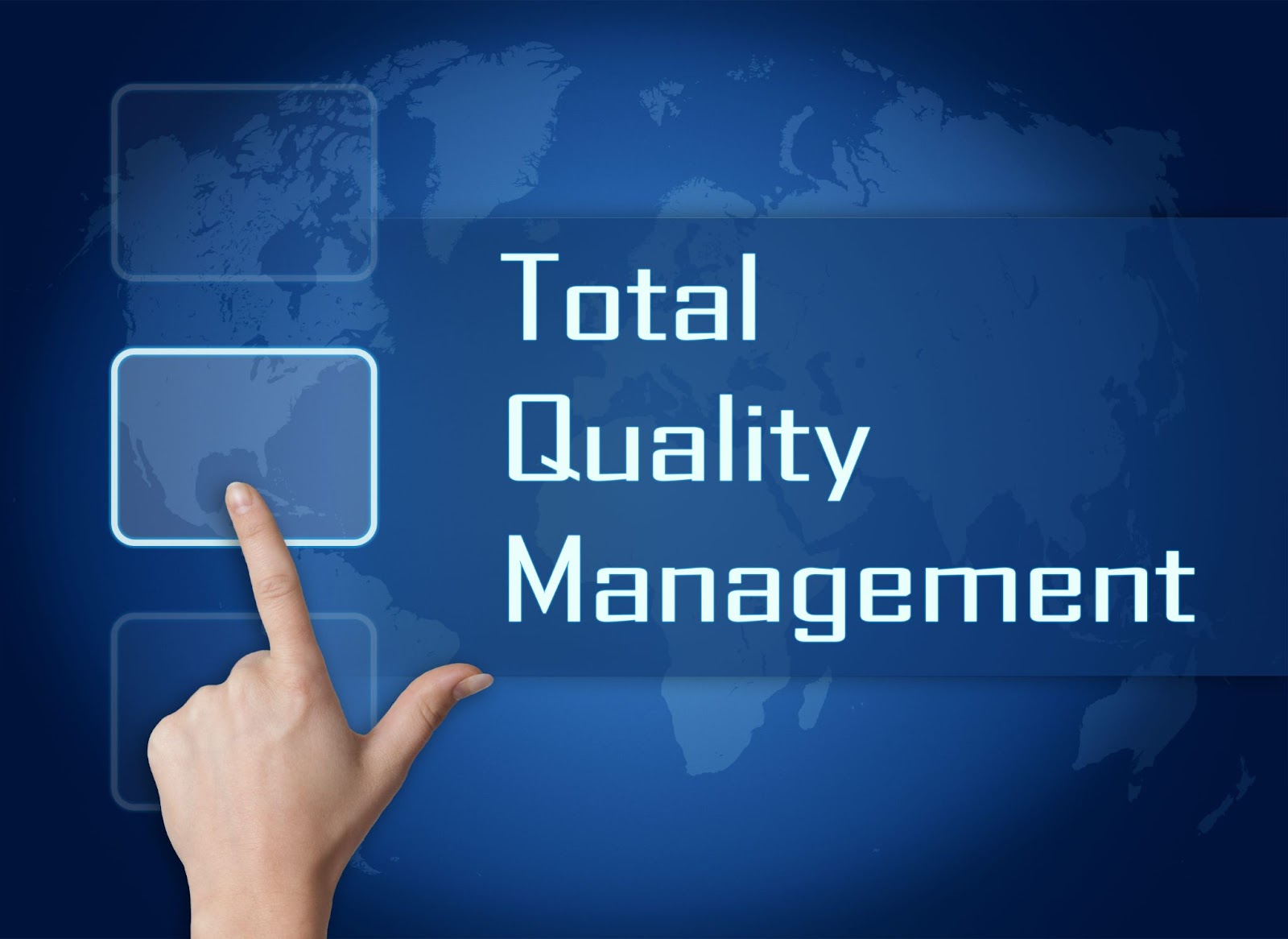
Many dynamics may influence the effectiveness of a project quality management program. Some barriers to successful TQM system implementation at construction organizations involve the very nature of the construction process. The projects are unique, locations vary, and work volume fluctuates. This is especially true if the work involves barriers such as more than one shift, quality personnel changes, labor-intensive work, a transient workforce, projects subject to delays, key supervision routinely changing, extensive supply chains, and differing visions, values, processes, and disciplines.
Silos are often set up, which can be driven by department, skills, certifications, or poor visionary leadership. Still, the most significant factor is the lack of comprehensive training that covers all disciplines. Typically, most companies buy into the notion that CWI certification covers all disciplines. The term CWI stands for Certified Welding Inspector. This certification and the training that goes into getting it is based on welding inspection alone. Granted, this training does provide the building blocks for other training. Nonetheless, Certified Welding Inspectors generally lack the skill set for Total Quality Management.
One of the critical tools in setting up a Total Quality Management program is the ITP (Inspection and Test Plan). This ITP document would have typical inspections and tests for each discipline in a complete EPC project, with most disciplines represented.
The Civil discipline, for example, includes:
This is just one discipline. What is the takeaway from that? A person trained in one discipline, such as welding, will not be adequate to perform these inspections or even to provide oversight to these activities when done by others, like a third-party company. To ensure that the resulting quality of the work will meet expectations, the workforce must be trained and qualified. This training should cover all disciplines. Another alternative is to ensure that those hired already have this training.
Effective Training Models: SNT-TC-1A and Business-Specific Curricula
An excellent program to use as a platform is SNT-TC-1A. Developing training structured around a visual acuity model is advantageous, which SNT-TC-1A offers. Another model is to develop a curriculum that best fits your business model. If that is the power sector, it would need one model type. If it is the Petrochemical model, then it would be adjusted to fit that industry. Either way, developing a training structure is the best and least expensive way to get your quality professionals the training they need to tackle whatever requirements a client will put before them.
As a Quality Director, I strive to train teams across all disciplines. For example, we have developed a Quality Management Academy that directly correlates to the work and clients we specifically support. This training includes 30 hours of classroom training, labs, and self-study with “Check your Learning” quizzes at the end of each module. I like to make it interactive by using a Jeopardy-style game that brings in a competition aspect by having teams compete against each other for the correct answer (see Exhibit 1). Labs are built around specific disciplines. For example, structural steel training includes the different bolting systems we deal with and hands-on training with a Wilhelm-Skidmore (see Exhibit 2), as well as a lesson from our Quality Professionals with practical applications.
The Positive Impact of Meeting Project Quality Requirements
Construction Industry Institute (CII) research (publication 10-2) estimated annual losses due to rework in industrial construction at $15 Billion. CII also estimated that losses could be as much as 12% of the total project cost. That is staggering. Installing work incorrectly has a clear tieback to the lack of training on those installing and inspecting the work. That last line of defense for any EPC is called Quality Assurance, and with $15 Billion of re-work, it shows it is not working when it counts. I believe a lack of training is part of the reason why.
Failure to meet project quality requirements can negatively impact the project delivery process. It creates extra work for the parties involved. It also can build a perception of the poor quality of a given contractor, which consequently has the most significant impact on the contractors’ ability to get work. Having Quality Professionals trained in Total Quality Management in construction will help mitigate rework and help build a quality culture that any client would appreciate and support. Training is the key to achieving this, and having pleased and repeat clients is the outcome.
For over 35 years, H+M Industrial EPC has provided specialized services in the EPC industry. We are confident that our experienced, highly trained team of qualified workers can meet your capital project requirements. If you'd like to learn more about total quality management in construction, contact us today!

The H+M Industrial Team
For over three decades, we have provided best-in-class capital project management services to Energy and Chemical industries through our proven EPC approach. We are dedicated to providing trust, experience, and efficiency through all stages of engineering, procurement, and construction--on budget and on time.
Partnering with H+M Modular
H+M Modular, a division of H+M Industrial EPC, specializes in custom fabricated equipment, modules, and skids for energy and chemical industries. The approach emphasizes the potential for decreased risk through more controlled fabrication, leading to enhanced quality and safety, reduced labor costs and construction times, improved labor availability, and solutions to geographic challenges. We are dedicated to providing trust, experience, and efficiency through all stages of traditional and modular construction projects using our proven EPFC approach, If you're considering modular fabrication, we invite you to connect with us to learn about how modular solutions can improve project outcomes.