Capital project owners are familiar with both EPC and DBB. However, the benefits of using EPC management methods may seem to be primarily in larger projects where there are areas to find efficiencies and the scale makes it necessary for singular responsibility. That simply isn’t true—even in smaller projects, having integrated processes from the design and construction stage can reduce schedules and limit communication issues.
Below, we describe some of the challenges with using the DBB process for managing capital project life cycles as well as how utilizing an EPC delivery method can streamline project management.
Challenges with Design-Bid-Build
Every construction project manager is familiar with Design-Bid-Build, as it’s the framework still used by most small and medium-sized industrial projects. That does not mean that having separate design, procurement, and construction stages always makes sense for many capital projects. To see why, you can look at the steps intrinsic to DBB construction projects, which follow:
- Concept/Feasibility
- Front End Engineering and Design
- Detail Design
- Procurement and Construction
Note: Depending on the size of the project, the steps may be combined or separated further with responsibility for each step assigned at varying degrees to the owner or contractor for that step.
In general, each one must be completed before any work can begin on the following stage. This can create a “silo” effect, especially if different organizations are involved. As an example, the designer may not know the construction contractor’s capabilities or techniques for build designs and decisions. This often leads to more change orders during the capital project life cycle as well as more capital expenditure.
In addition, by not incorporating construction experts during the design phase, the client must trust the engineering and construction contractor will have the in-house expertise or else expect increases in project duration. The owner also must manage the project’s delivery during the entire capital project life cycle, with the potential for risk occurrence at each gate.
EPC Benefits for the Capital Project Life Cycle
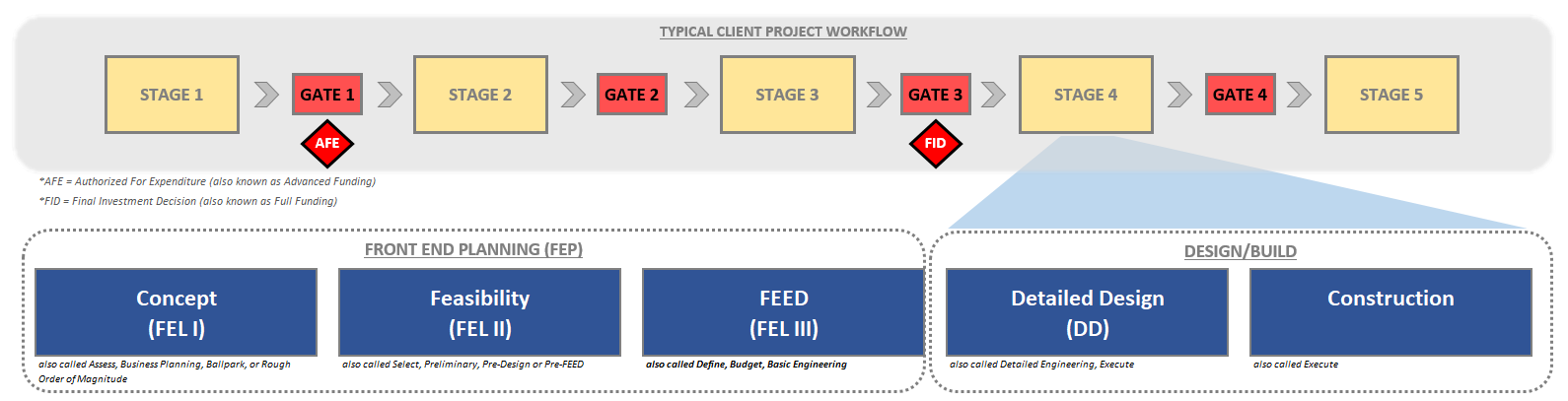
The bidding process can cause a major schedule sink, especially when combined with the disparity between design goals and construction contractor capabilities. EPC benefits begin by eliminating that key project gate through overlapping project stages.
Imagine a scenario where a project requires a specialized fitting or another element. An integrated project team will be able to incorporate this time into the schedule and begin fabrication at a machine shop upon client approval, instead of waiting for the procurement team to run down options and then asking an outside firm to create the same component. A design team that understands that an element requires hazardous work can alert the construction team to ensure the set-up of the proper environment or propose alternatives when they’re feasible.
This sort of iterative process is focused on making the most use of EPC management techniques during the capital project life cycle by limiting movement and waste or minimizing their impact on the schedule where possible.
Working with one entity provides a valuable benefit to project owners—a single point of accountability. There is only one organization to interface with over budgeting issues or managing any unexpected events.
How to Select an EPC Contractor
In large part, a project owner has experience in knowing what criteria to look for in an EPC contractor to ensure project success, including proven delivery and capability. While it may seem like many EPC contractors provide similar services, they can differ with the answers to the following questions:
- Do they handle their own construction and fabrication? Many firms that bid on EPC projects do not have an extensive construction department and must subcontract out certain elements of a design. Many must also outsource specialty fabrication work.
- What safety and quality controls exist? An experienced EPC contractor has systems and documented processes across the entire capital project life cycle. This is critical for health, safety, and environmental concerns where a simple design feature might require high-risk work and extend project schedules.
The EPC process only works as well as the people who are utilizing it to complete a project. So in addition to other means of due diligence, ensuring that there is great cross-departmental communication can ensure better project results.
Why EPC is an Effective Solution for Smaller Projects
A smaller budget generally does not mean smaller expectations—often, it’s the opposite. A short-term project of a few months is crucial to guarantee a facility’s uptime, as an example. The ability to work with one entity throughout the capital project life cycle during projects of any size improves delivery certainty.
By incorporating constructability into the design phase and ensuring that procurement and equipment issues with long lead times can be addressed early on, schedule uncertainty is minimized to the greatest degree possible. This means better inherent project quality because the same groups can communicate with each other across project stages and have a deeper understanding of each others’ capabilities.
Ensure Capital Project Life Cycle Success with H+M Industrial EPC
Quality and safety controls through the capital project life cycle start with a top-to-bottom commitment. The contracting solutions offered by H+M Industrial EPC integrate the design, engineering, fabrication, and construction within our organization. Your project deserves one entity that can integrate project stages to maximize your budget and ensure that your goals are met on schedule.

The H+M Industrial Team
For over three decades, we have provided best-in-class capital project management services to Energy and Chemical industries through our proven EPC approach. We are dedicated to providing trust, experience, and efficiency through all stages of engineering, procurement, and construction--on budget and on time.
Partnering with H+M Modular
H+M Modular, a division of H+M Industrial EPC, specializes in custom fabricated equipment, modules, and skids for energy and chemical industries. The approach emphasizes the potential for decreased risk through more controlled fabrication, leading to enhanced quality and safety, reduced labor costs and construction times, improved labor availability, and solutions to geographic challenges. We are dedicated to providing trust, experience, and efficiency through all stages of traditional and modular construction projects using our proven EPFC approach, If you're considering modular fabrication, we invite you to connect with us to learn about how modular solutions can improve project outcomes.