This webinar is ideal for professionals involved and/or responsible for project progress tracking: Project Managers, Project Engineers, Construction Managers, Construction Engineers, Project Controls Personnel, etc.
Project controls in construction refers to the processes and tools used to gather data, plan, monitor, and control each phase of a capital project. This article and webinar will review what is necessary to include in a Request for Proposal (RFP) in terms of project controls in construction and how to monitor progress via contractor-provided reports.
While project controls in construction are oftentimes associated with the execution or construction phase of the project life cycle, it’s important to understand that project controls also play a critical role in the pre-contract and bid phase.
A Work Breakdown Structure (WBS) is the key organizational hierarchy that syncs a project’s cost, schedule, and performance against a budget for each level of the WBS. A WBS contains 100% of the work defined by the scope or contract and captures all the deliverables that need to be completed. This is required for all projects despite their size. It’s critical to have the WBS defined pre-award for bid documents. The WBS also allows contractors to progress the project appropriately and effectively.
The Project Management Institute (PMI) identifies a few “core characteristics” of an effective WBS. These elements/rules include:
- Needs uniqueness
- Needs to be summative
- Each element should have a unity of responsibility
- Establishes motivation by involvement
- Has precision and assurance of all documentation
- Has consistency of definitions
- Needs to have easy utility
- Needs to be approved by all parties
To learn more, get answers to frequently asked questions, and take a look at an example, watch this part of the webinar where H+M Industrial EPC, breaks down a sample WBS.
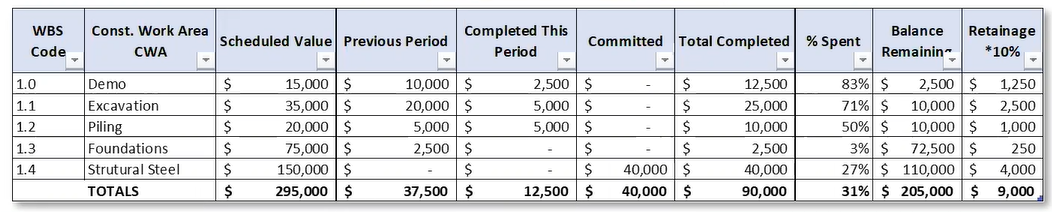
The Schedule of Values is an allocation of the entire contract sum along various portions of the work that will align with the WBS. A Schedule of Values should be used on more complex and high-value projects as well as multi-phase projects (multiple execution phases). This is generally applicable to projects with an approved budget. Project owners will use it to manage cash flow and contractor (progress) payments.
To learn more, answer frequently asked questions, and take a look at an example, watch this part of the webinar where Bill Gassmann, Director of Estimating at H+M Industrial EPC, explains an example of a Bid Breakdown and Schedule of Values.
When owners receive bids from contractors as part of the pre-bid phase, it’s important to request a Contractor Rate Sheet. Contractor Rate Sheets provide owners with a basis for the contractor's bid. This allows owners to evaluate rates in comparison to competing contractors. It also:
- Allows for easy identification of reimbursable costs during execution
- Billing/invoice validation of costs
- Helps in the support of potential changes during project execution
Owners should request a Contractor Rate Sheet as a separate exhibit within the RFP to keep everything uniform and easy to access. Most contractors will have a predefined Microsoft Excel sheet with their rates that can be easily manipulated into the format you request. Having a predefined listing of small tools and consumables/supplies to provide to the contractor helps with transparency and communication between the owner and contractor while also identifying what should be included. The standard mark-ups for third-party costs should also be included in the Contractor Rate Sheet.
A project execution plan (PEP) is the primary document that establishes and outlines a contractor’s means to execute, monitor, and control a project. This should contain an overview of all components of the project's scope of work and highlight the critical path for the project. The PEP should be the basis for the project’s baseline schedule, which allows the contractor to develop detailed reports for which progress is measured.
Project Reporting Schedules are listings that refer back to different sections/exhibits within the contract or Request For Proposal documents to highlight reports and deliverables required by the contractor. This will include the type, format, and frequency it will be provided, along with any other comments or notes you want them to provide. Owners typically have internal reporting cycles, so this will be a good place to identify these cycles to work out scheduling issues. It’s important to set expectations contractually and align the contractor with the owner's reporting cycle requirements.
In this part of the project life cycle, there is a lot of interaction between the estimates pre-determined in the last phase and projectable items with tracking/reporting.
Earned Value Management is defined by the PMI as a project management methodology for objectively measuring project performance using an integrated schedule and budget based on the project WBS. Typically, the project budget is rolled-up and weighted values are assigned while direct labor may be weighted based on total man hours instead of total dollars.
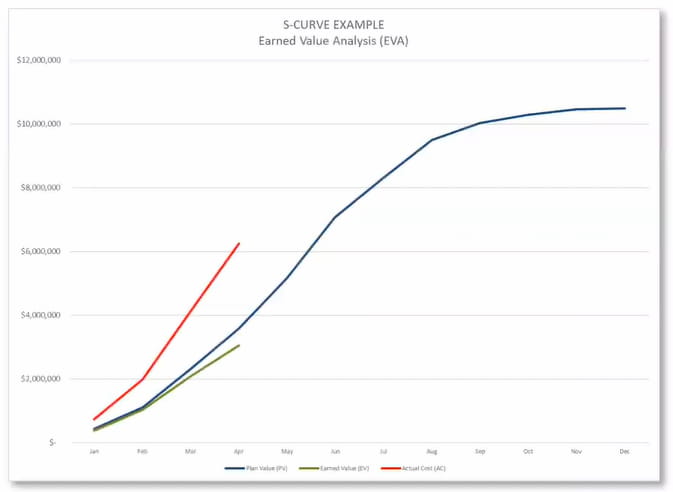
A contractor typically will use rules of credit to define the earning rules for project activity. Rules of credit are predefined, agreed-to steps with weight values that must be met to determine incremental progress by activity.
To learn more and take a look at an example, watch this part of the webinar where H+M Industrial EPC, navigates an earned value analysis.
The reports that a contractor, particularly for a reimbursable project, should provide to an owner routinely include a progress measurement report, manpower histograms, quantity curves, performance reports, daily head count, a cost report or simple cost breakdown, and a cash flow report.
The progress measurement report is the most critical report to receive from a contractor. This report will identify a contractor's percent plan complete (PPC), their actual percent complete, and their forecast to finish the project.
The manpower histogram identifies how many people the contractor intends to have out at the site. It can help determine schedule, safety, rules, and other vital elements to project completion.
Quantity curves (or commodity curves) track quantities on a project. These elements include dirt, concrete, structural steel, number of terminations, and more. This report helps to identify the progress of a project.
Performance reports are also very critical for contractors to provide to owners. These reports will calculate the earned and actual productivity of a contractor. The contractor calculates performance by taking earned hours and dividing them by the actual hours spent.
The daily head count, also known as the on-premise report, gives owners an idea of how many people are on-site each day. It's important to understand who is coming in and out of the site for the billing cycle.
The cost report or cost breakdown would be similar to the Schedule of Values. It identifies that your contractor is managing finances and helps you understand what is remaining within the budget.
The cash flow report is the projected cash flow. This should include information on how the contractor plans to invoice you as well as a representation of progress to determine if the contractor is on track with the plan.
To get a deeper understanding of these reports with examples, watch this part of the webinar.
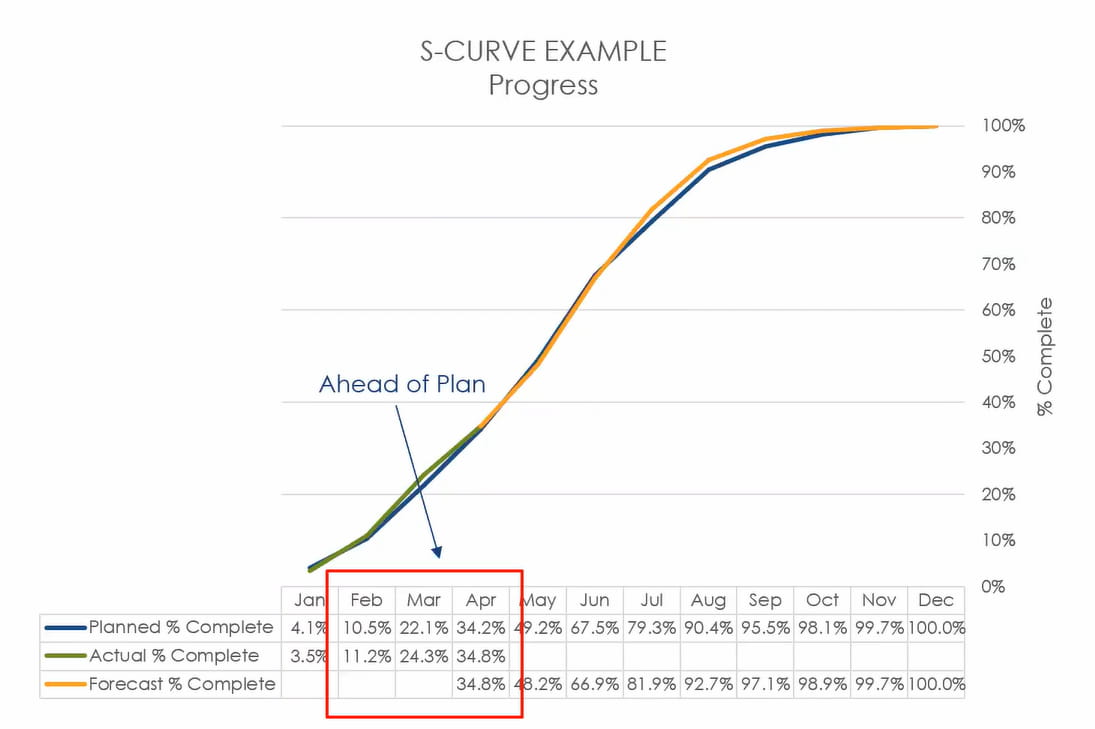
S-Curves are graphical tools used for planning, monitoring, controlling, analyzing, and forecasting project status, progress, and performance. They represent a project’s progress of work over time and form a historical record of trends and disparities for the contractor to analyze in future projects.
S-Curves are used in many instances as a project management tool. Some of the most common uses are for progress and performance evaluation, quantity installation, and cash flow forecasts.
To learn more about S-Curves and how to read them through examples, watch this part of the webinar.
It’s important for governing documents/contracts to identify the specifications required by a contractor to notify the owner of, given any potential changes. Also, developing an effective workflow for processing changes is important to maintain connections and honesty between the owner and contractor. This can be done by establishing recurring meetings to discuss changes or allotting time during existing meetings to discuss.
The important and standard criteria and information that an owner should receive from a contractor related to each change request includes:
All of this information should be cataloged into a regular issuance of a project change log.
It’s important to maintain updated project budgets and quantities as the changes are accepted/approved. This limits delays and helps improve the accuracy of progress reporting. This also allows for the project execution plan and schedule to reflect any new changes.
To learn more about how changes can impact reporting with examples, watch this part of the webinar.
H+M Industrial EPC values our client-owner relationships, and we encourage transparency and communication. By providing project controls in construction, we hope to plan and execute your capital project successfully.

The H+M Industrial Team
For over three decades, we have provided best-in-class capital project management services to Energy and Chemical industries through our proven EPC approach. We are dedicated to providing trust, experience, and efficiency through all stages of engineering, procurement, and construction--on budget and on time.
Partnering with H+M Modular
H+M Modular, a division of H+M Industrial EPC, specializes in custom fabricated equipment, modules, and skids for energy and chemical industries. The approach emphasizes the potential for decreased risk through more controlled fabrication, leading to enhanced quality and safety, reduced labor costs and construction times, improved labor availability, and solutions to geographic challenges. We are dedicated to providing trust, experience, and efficiency through all stages of traditional and modular construction projects using our proven EPFC approach, If you're considering modular fabrication, we invite you to connect with us to learn about how modular solutions can improve project outcomes.