Remote IO Cabinets versus Junction Boxes in Industrial Control Systems
With the modern advances in control systems architecture and communications protocols, the technology available to us today is leaps and bounds above what it was in the era of relay and timer logic as well as the first few generations of Programmable Logic Controllers (PLC). Given the tools available to us today, isn’t it time we realign our thinking when it comes to the practical implementation of control systems? The days where we were required to house all of the control systems hardware components in a centralized location are no more. Improvements in the efficiency, reliability, redundancy, and cost of networking components have allowed us the opportunity to provide a more robust, expandable, and cost-effective design.
In earlier iterations of industrial control system solutions, the flexibility of the installation was limited by the type of communications used. In most cases, these used a type of serial communications which is extremely limited in speed and distance in comparison to the modern-day performance of PLCs. With the ever-growing rates of data transfer and speeds at which the data is needed diminishing, the only way for continued growth is to advance to faster, more efficient communications protocols such as Ethernet/IP. Imagine attempting to pull up real-time data on a turbine running at 10,000+ RPM on an RS-232 serial communications interface, or to put it in modern terms, attempting to watch your favorite cat video on the internet via a dial-up internet connection. In one case, you’ll have to wait a very long time to see the cat; in the other case, there could be a catastrophic failure on the order of millions of dollars due to the latency in response time. However, with the speeds and distances which are achievable with modern copper and fiber Ethernet communications, limitations for where PLC hardware is located is no longer an issue.
In a traditional PLC design, a typical implementation for a large industrial facility was to have several locations (junction boxes) scattered throughout the facility where field instrumentation would be wired via individual cables. These junction boxes serve as a splice point to allow for larger multi-pair or multi-conductor (home run) cables to connect back to the central control system cabinet which held the marshaling terminals and PLC hardware. With this method, each cable running to an end device had at least 4 terminations (at the PLC, at the home run side of the junction box, at the field side of the junction box, and at the end device). This means that there are at least two added points of failure or potential for error for every single conductor. With almost any modern PLC, we can now locate IO modules remotely in the field (remote IO or RIO cabinets). Rather than having multiple single points of failure in each cable, we can build redundancy in the communications architecture of the PLC system and almost entirely remove a potential for having a single point of failure. As one can see in figures 1 and 2 below, the traditional junction box design has twice the number of terminations as a RIO cabinet design. Additionally, if any one of the blue cables were cut, there would be a failure on multiple instruments. With a RIO cabinet design, if any of the red cables were to be cut, there is no loss in data as this is a redundant ring type of network. From an expandability standpoint, when a traditional junction box design requires expansion, multiple large cables must be run at potentially long distances to connect the new field IO to the main PLC. In order to bring field IO to the main PLC with a RIO cabinet design, all that need be run is two small communications cables regardless of the size of the expansion.
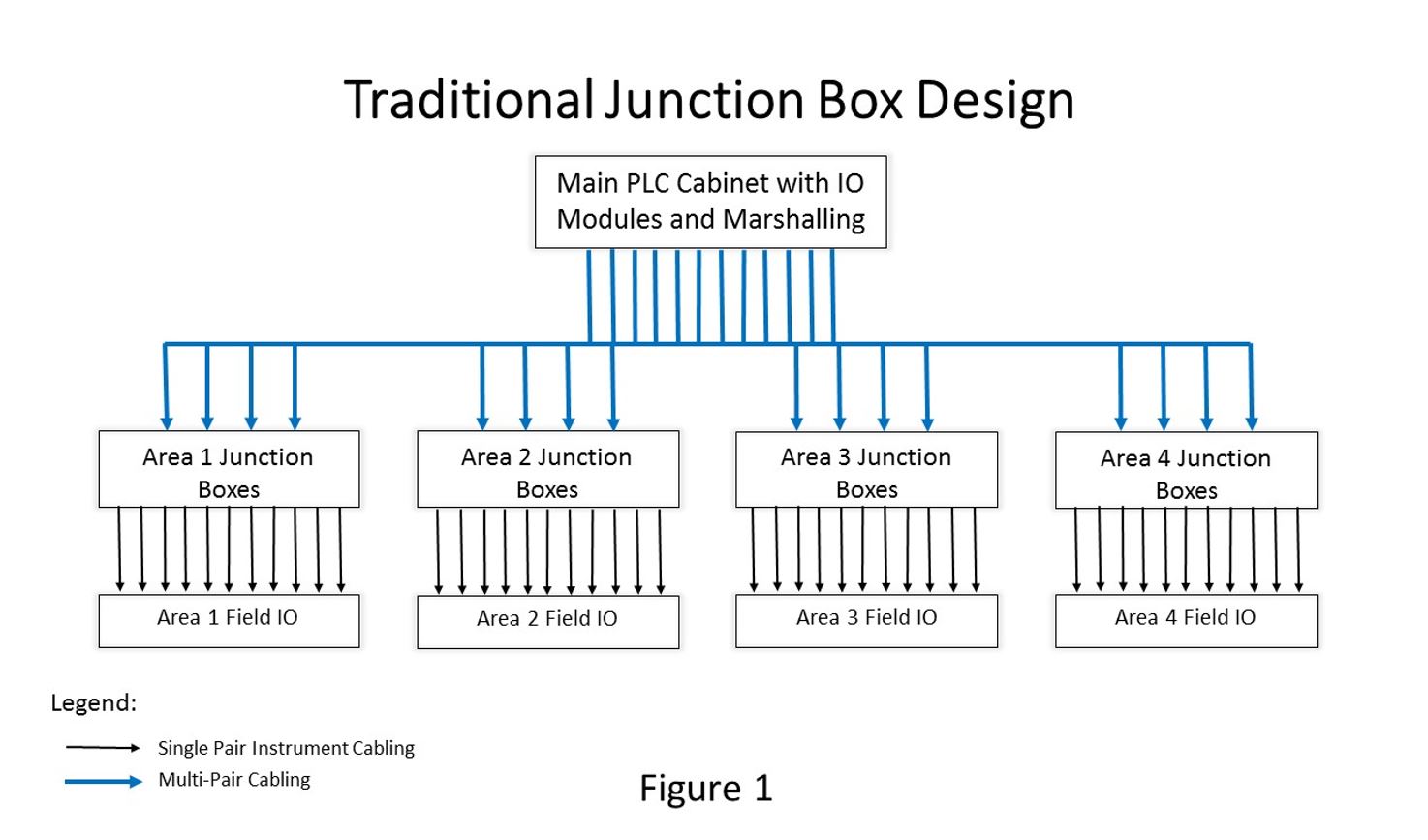
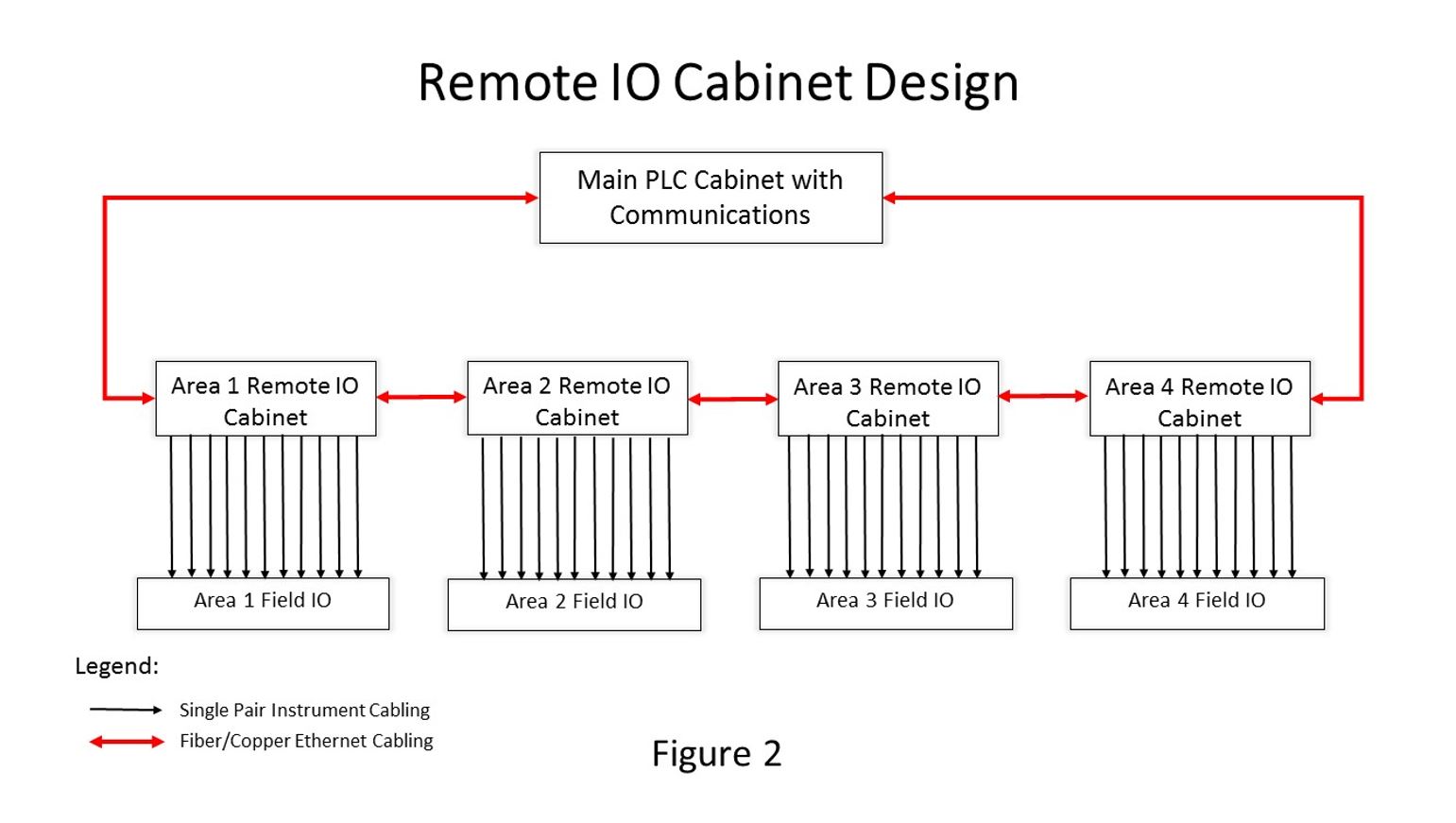
As with most design implementations, an ever-present determining factor is cost. On the surface, it may seem that a RIO cabinet design is more costly due the additional networking components required. It is true that additional Ethernet and fiber cards, patch panels, and switches are needed; however once construction is factored in, the overall cost is much less. In the above example figures, the cost of the PLC hardware is very similar, the only significant cost differences being additional communications cards and power supplies. The enclosures required for the RIO cabinets are larger than traditional junction boxes and also typically must be purged with dry air or nitrogen if located in a hazardous (electrically classified) location. When comparing the cost of only the PLC hardware, enclosures, and communications components, the cost for the RIO cabinets will be roughly 10% more depending on the size of the implementation. When comparing the cost of the cabling, conduit, cable tray, bulk construction materials, and labor, there is a cost savings with a RIO implementation on the order of 30-50%. One can see this when comparing the size and magnitude of terminations and cables between Figures 1 and 2 (red versus blue cables). In a junction box implementation, there is a minimum of 4 additional terminations per IO. This cost is magnified when considering all of the additional cabling and raceways it takes to wire between the junction boxes and PLC cabinet. All of these factors result in additional field labor and consumable construction materials.
When comparing all factors of a traditional implementation with a RIO cabinet implementation, there really is no comparison. With the speeds and fault-tolerant construction of modern networking components, the drawbacks of relying on a network are all but gone. The expandability of a networked control system is very flexible and nearly limitless without the worry of needing excessive raceway space. Add these factors to the fact that the total installed cost of a RIO system is much less than that of a junction box design and it is hard to argue why one wouldn’t choose a RIO system.

The H+M Industrial Team
For over three decades, we have provided best-in-class capital project management services to Energy and Chemical industries through our proven EPC approach. We are dedicated to providing trust, experience, and efficiency through all stages of engineering, procurement, and construction--on budget and on time.
Partnering with H+M Modular
H+M Modular, a division of H+M Industrial EPC, specializes in custom fabricated equipment, modules, and skids for energy and chemical industries. The approach emphasizes the potential for decreased risk through more controlled fabrication, leading to enhanced quality and safety, reduced labor costs and construction times, improved labor availability, and solutions to geographic challenges. We are dedicated to providing trust, experience, and efficiency through all stages of traditional and modular construction projects using our proven EPFC approach, If you're considering modular fabrication, we invite you to connect with us to learn about how modular solutions can improve project outcomes.